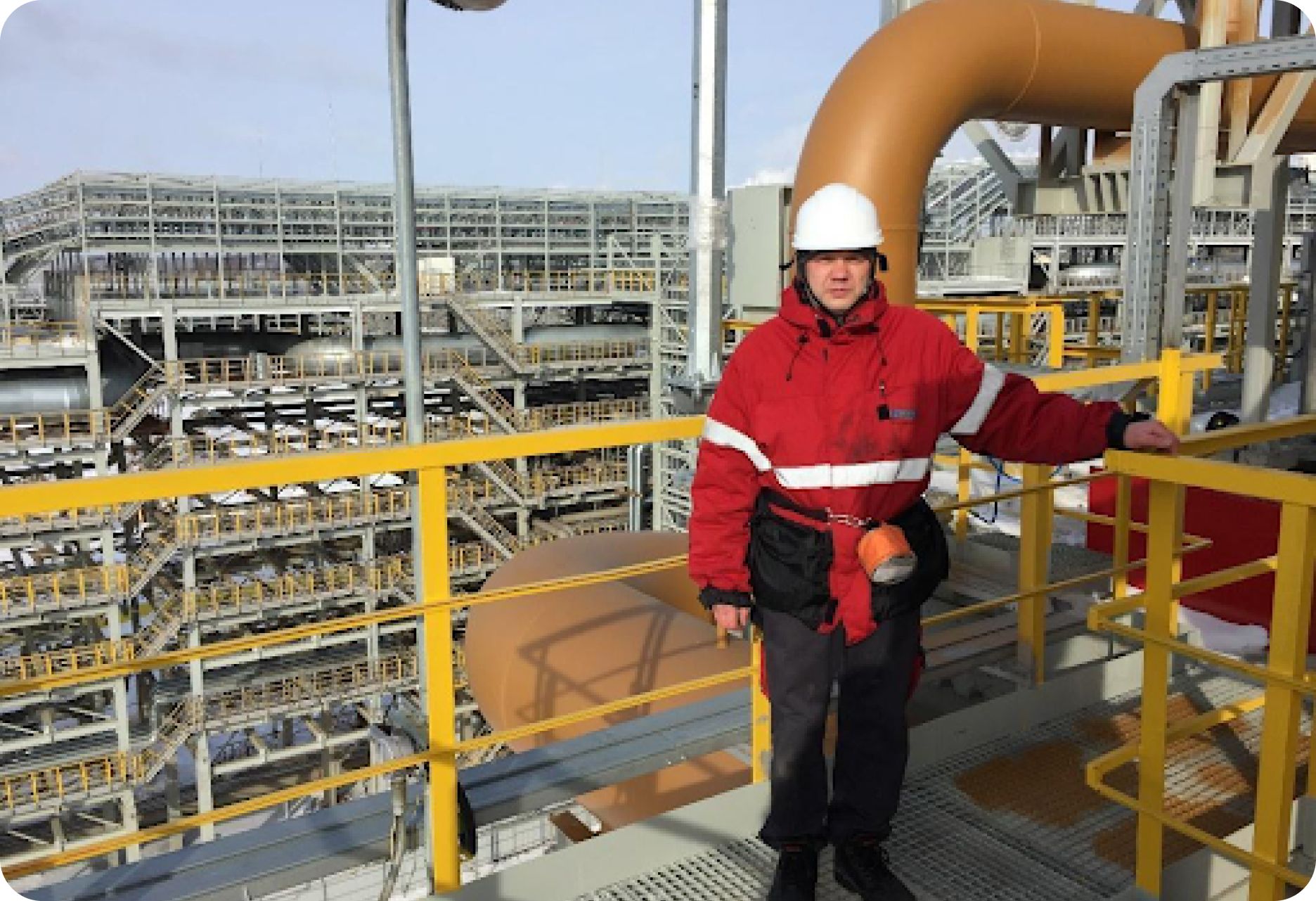
One of the enterprises raised the issue of rotor equipment reliability - NEDS 100-160 pumps were systematically failing. After analysis, the following problems were identified: bearing mounting quality, coupling, vibration, alignment.
The alignment was carried out using the VIBRO-LASER shaft alignment and geometry measurement system.
The alignment check showed no deviations from the alignment tolerance, the mounting of the bearings and coupling also showed no mounting defects.
A few days later, a vibration test was performed and the results showed signs of misalignment. An alignment check with VIBRO-LASER showed a deviation of about 1 mm. At the customer's request, we checked the alignment using clock-type indicators and a competitor's device (a well-known brand manufactured in Germany). The measurement results were similar. From the very beginning it was clear that the piping would influence the alignment, but nobody assumed that the alignment would be significant.
We decided to install supports under the piping (check photo 3) on some of the pumps and to purchase alignment devices. In terms of price and quality it was decided to buy VIBRO-LASER «STANDART» configuration. Some may argue that the German device is more functional and have advanced sensor... But the objective reality is that for "simple" equipment with couplings, such as pumps, fans, drives, etc., advanced functions are redundant and you have to overpay for them by 1.5-2 times. Applying logic, you can cut linear sensors ("strips") of more than 10 pieces from a 2D matrix ("square"), you can also use a workpiece with damaged sectors. Therefore, the use of simpler sensors is economically justified.
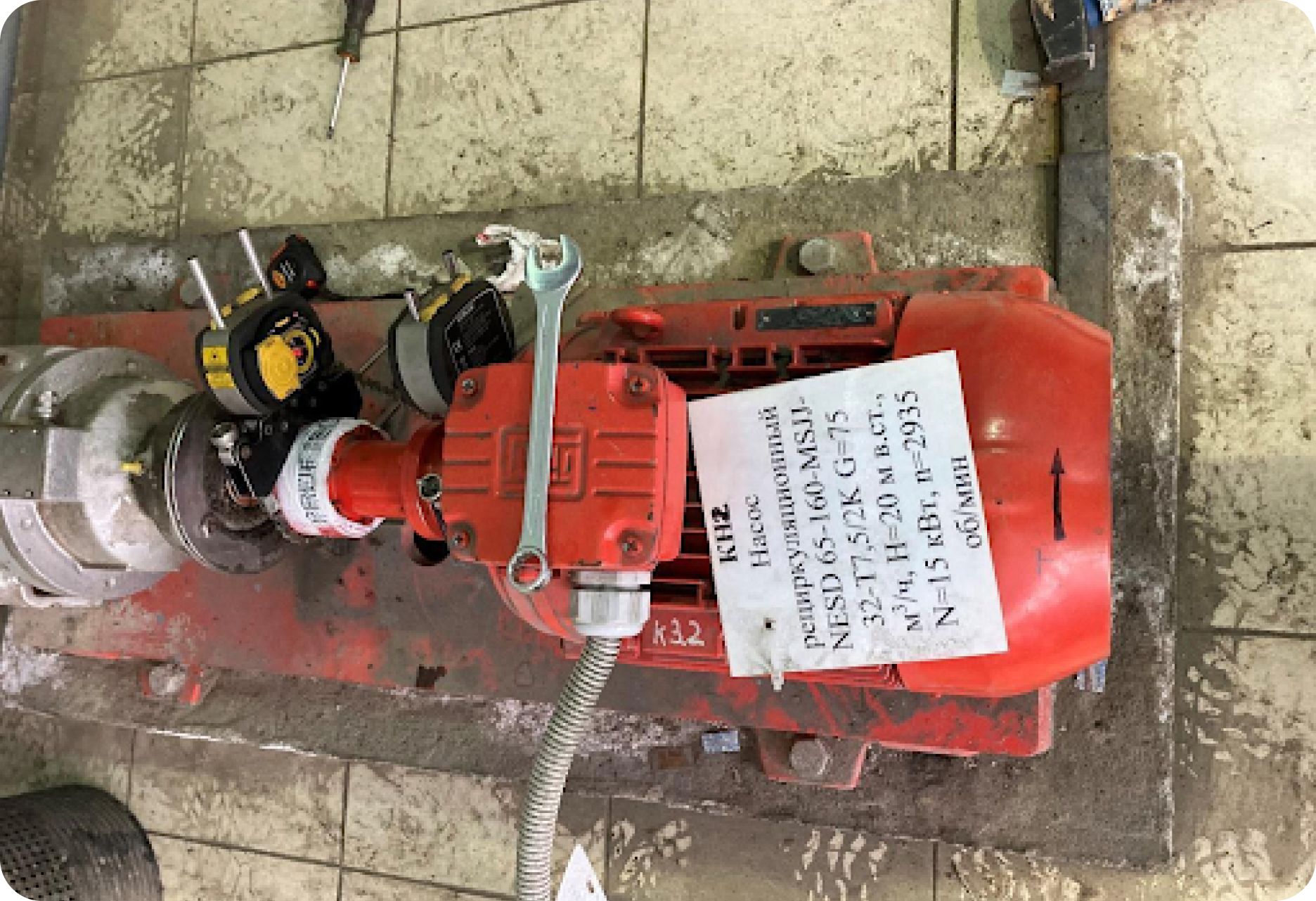
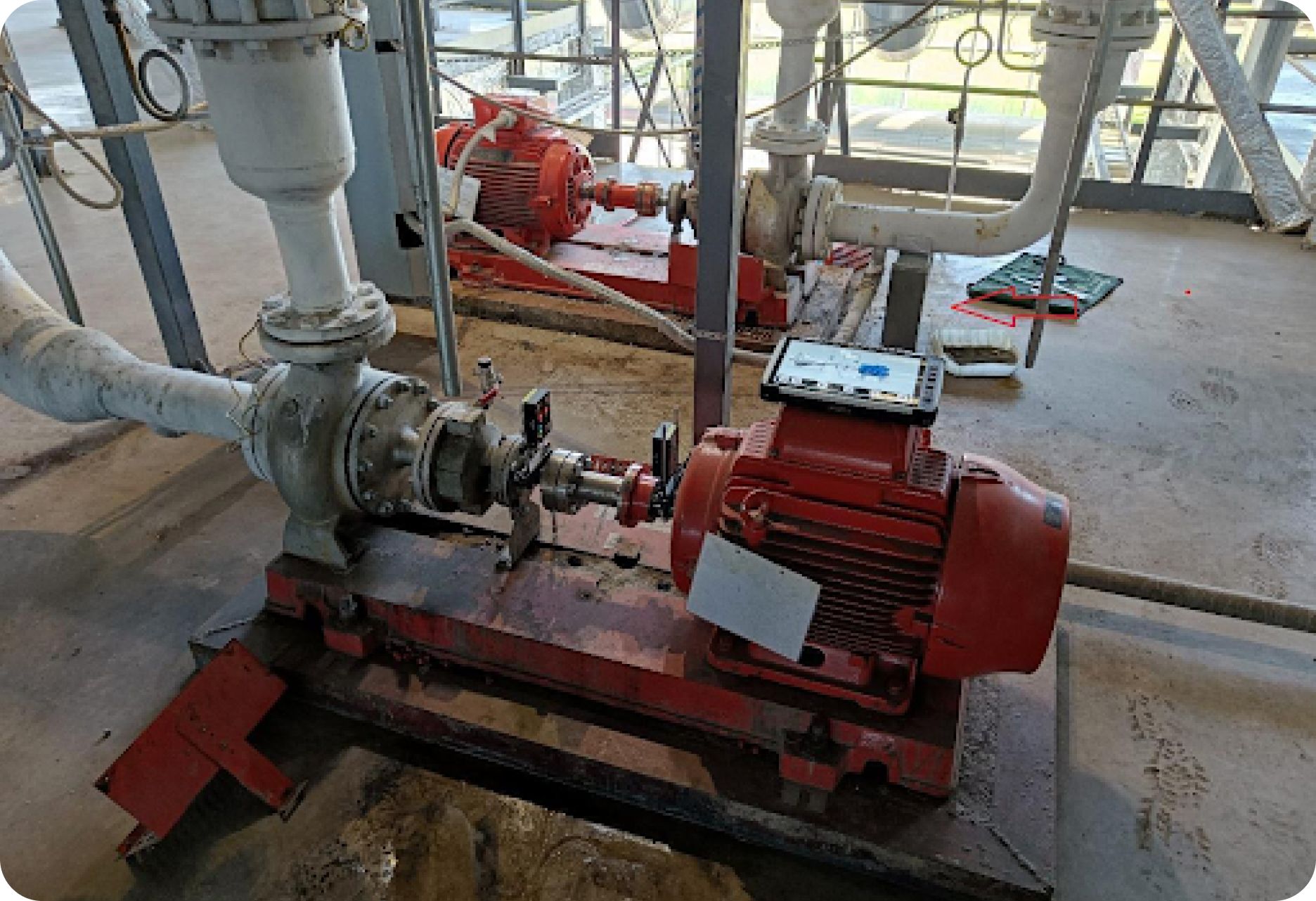
In addition, repair and calibration of a complex optoelectronic sensor (if it has not been calibrated) can only be performed in Germany, which is associated with significant costs.