Innovative Methods for Pipeline Diagnostics and Alignment
Limitations of Traditional Pipeline Maintenance Approaches
Modern industrial facilities and infrastructure networks require high reliability and efficiency in their operation. One of the key factors influencing the longevity and uninterrupted functioning of pipelines is the timely detection and elimination of defects. Traditional maintenance methods often lack the precision needed to identify issues early, leading to increased repair costs and a higher risk of critical failures. However, advanced technologies such as vibration diagnostics and laser alignment significantly enhance equipment monitoring, minimize operational costs, and improve overall system performance.
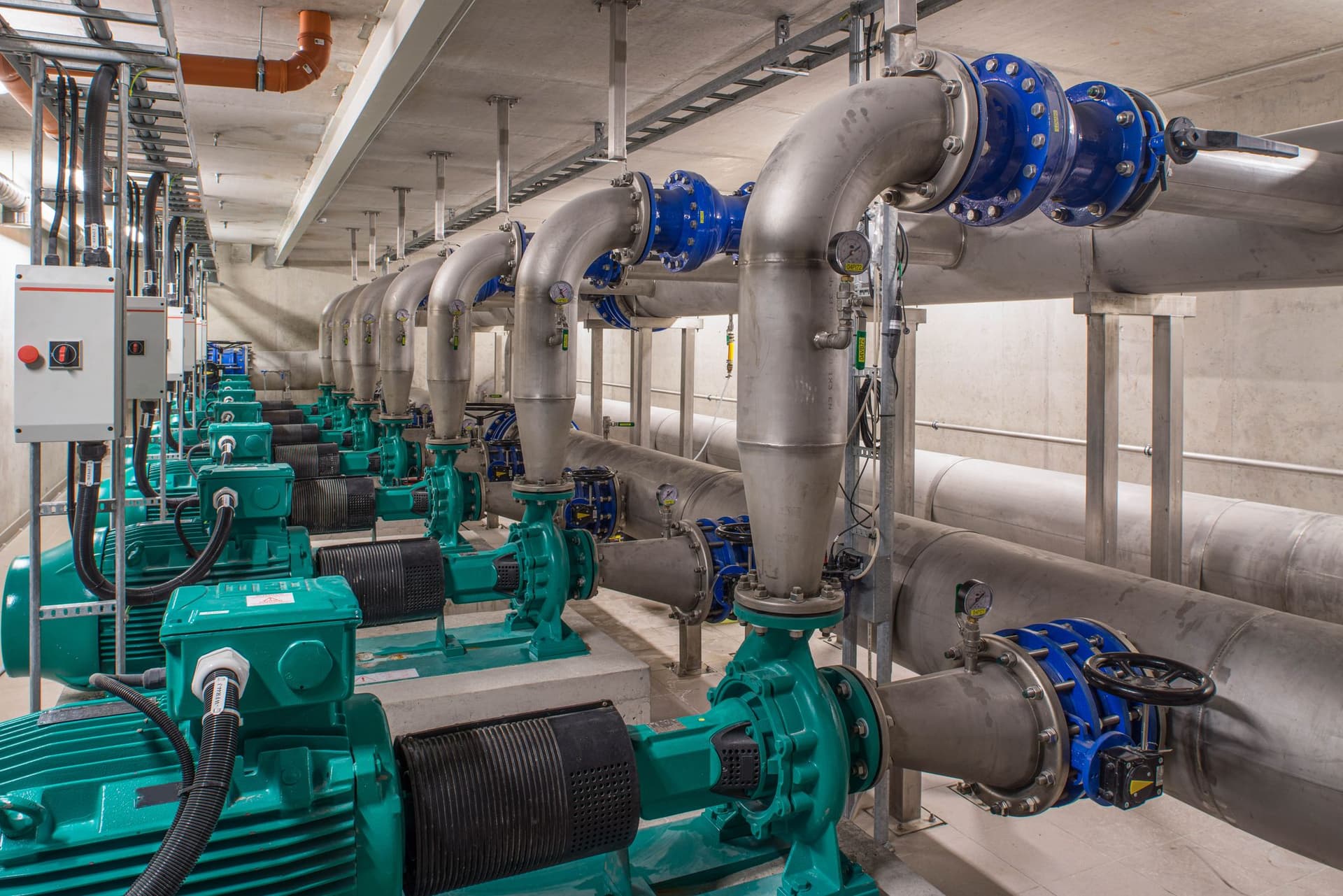
Traditional maintenance methods often lack the precision needed to identify issues early, leading to increased repair costs and a higher risk of critical failures.
Many enterprises continue to rely on outdated preventive and scheduled maintenance techniques, but these methods come with significant drawbacks: inability to detect minor defects in time, which may lead to major failures in the future, increased costs for urgent repairs and equipment replacements in the event of breakdowns and extended downtime due to unscheduled maintenance work, negatively impacting productivity.
By integrating innovative monitoring techniques like vibration diagnostics and laser alignment, companies can mitigate these risks and ensure the stable operation of pipeline systems.
Vibration Diagnostics: A Modern Predictive Analysis Method
Vibration diagnostics is a monitoring technique that analyzes mechanical vibrations to detect potential faults at an early stage. This predictive maintenance method offers several advantages: detection of hidden defects such as identifies cracks, bearing wear, pump imbalance, and other mechanical faults long before they become critical, prevention of emergency situations via continuous monitoring of vibration characteristics reduces the likelihood of unexpected system failures, reduction of maintenance costs and extended equipment lifespan with timely identification and correction of problematic areas enhance the durability of the entire system.
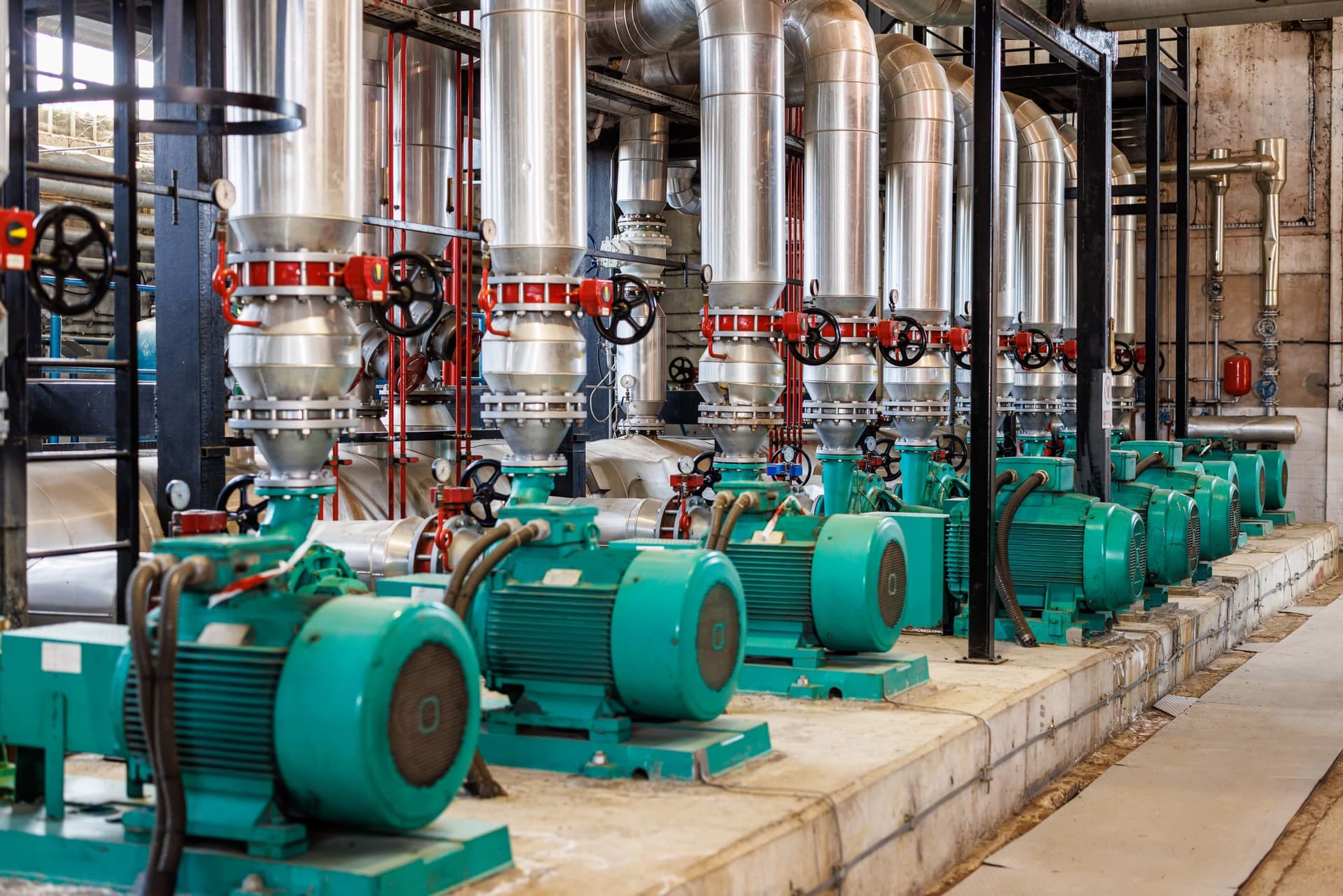
How Vibration Diagnostics Works
Vibration diagnostic equipment consists of sensors that measure the amplitude and frequency of vibrations. The collected data is analyzed using specialized software that identifies deviations from normal operating conditions. Modern vibration diagnostics systems operate in real time, allowing for immediate responses to changes in pipeline conditions and associated machinery.
Laser Alignment: Precision for Stable Performance
Laser alignment is used to adjust pumps, compressors, electric motors, and other machinery connected to pipeline networks. Proper alignment of mechanical components reduces stress on joints, minimizes vibration, and enhances overall system reliability.
Key benefits of laser alignment:
- High precision. The technology achieves alignment accuracy down to microns.
- Reduction of vibrations and mechanical wear. Optimal configuration decreases stress on components and extends their service life.
- Lower maintenance costs. Prevents premature equipment deterioration and reduces the need for frequent repairs.
- Improved energy efficiency. Proper alignment reduces power consumption and enhances system performance.
How Laser Alignment Works
Laser alignment relies on high-precision laser measuring instruments that detect even the slightest deviations in equipment positioning. Operators receive real-time data, allowing for immediate adjustments. This method is far more effective than traditional mechanical techniques, as it reduces setup time and delivers superior accuracy.
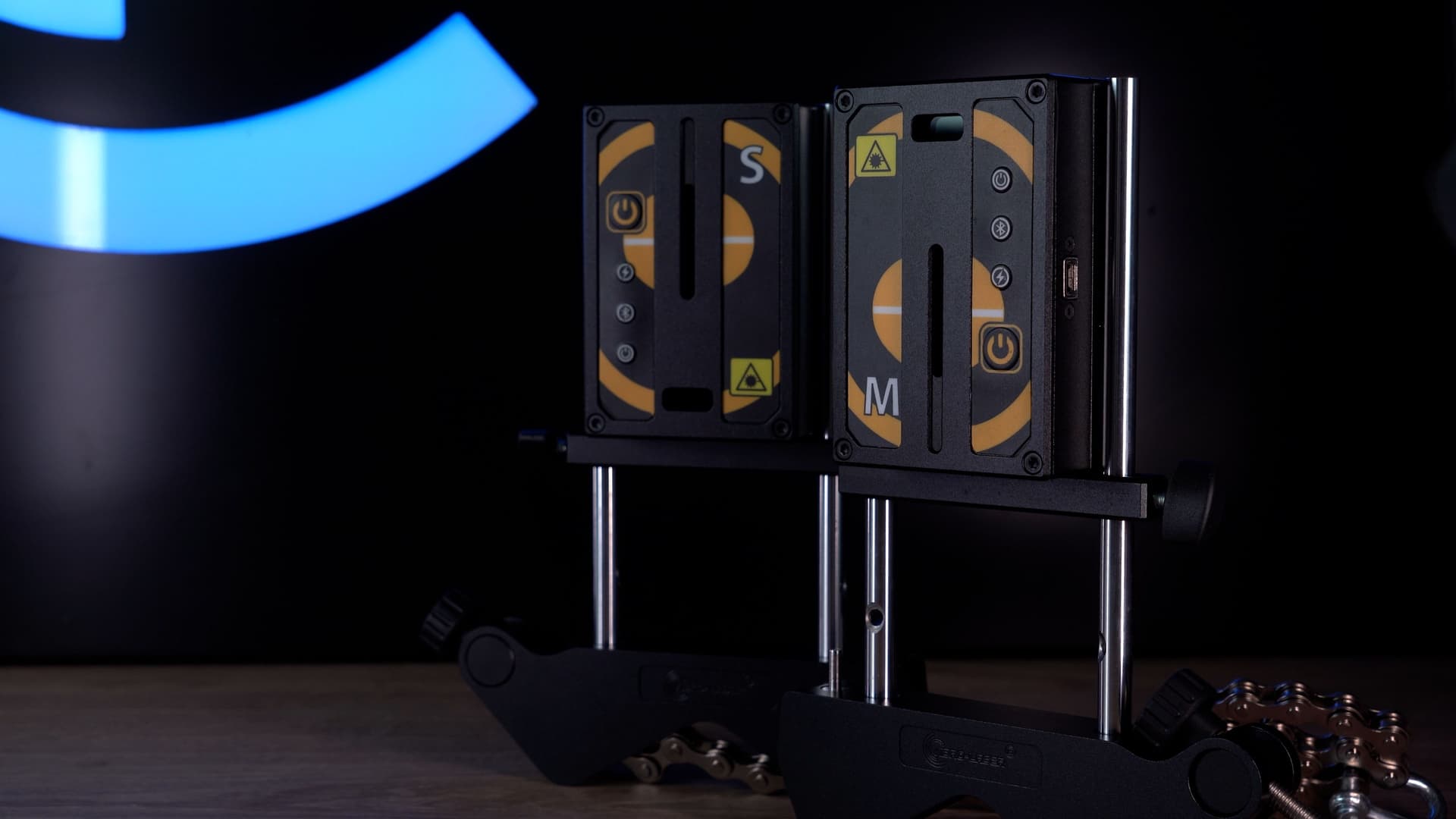
Conclusion
Implementing vibration diagnostics and laser alignment empowers companies to significantly enhance the reliability and efficiency of pipeline systems, proactively preventing critical failures before they escalate into costly breakdowns. These state-of-the-art technologies not only optimize maintenance strategies by reducing unplanned downtime and repair expenses but also extend the lifespan of essential industrial infrastructure. By ensuring precise alignment and real-time condition monitoring, businesses can minimize energy losses, improve equipment performance, and maintain seamless operations with maximum efficiency. Investing in advanced diagnostics and alignment solutions is no longer just an option—it’s a strategic necessity for industries seeking to achieve sustainable, high-performance production with minimal risk and maximum cost savings.
Investing in advanced diagnostics and alignment solutions is no longer just an option—it’s a strategic necessity for industries seeking to achieve sustainable, high-performance production with minimal risk and maximum cost savings.